En su norma A3.0M/A3.0:2010, la Sociedad Estadounidense de Soldadura (AWS) especifica, entre muchas otras definiciones, un listado completo de los más de 80 procesos de soldadura existentes hasta la fecha, desde los más populares, como las diversas variantes de la soldadura por arco (con electrodo metálico revestido, con electrodo de tungsteno protegida con gas, con núcleo de fundente o con electrodo metálico protegida con gas) hasta los menos conocidos o ya obsoletos (como soldadura por resistencia, soldadura de estado sólido, ambas mencionadas brevemente en este artículo, soldadura con oxígeno y gas combustible, o soldadura aceroacetilénica).
Sin embargo, la nutrida variedad de los procesos que abarca la norma A3.0M/A3.0:2010 no termina allí. En DeMáquinas y Herramientas ya hemos presentado varias notas referidas a otra tecnología de actual relevancia, como lo es el corte térmico, ya sea por plasma u otros métodos.
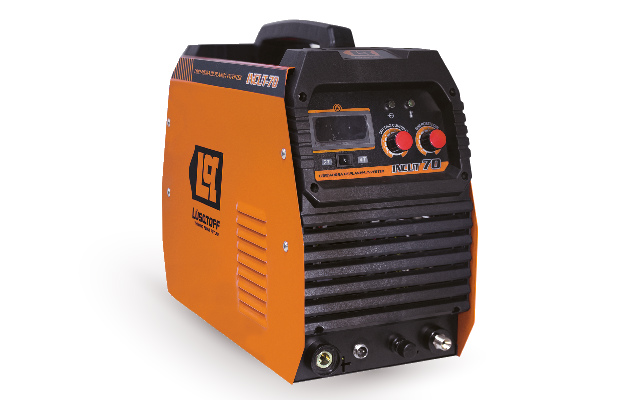
Cortadora de Plasma Inverter
También nos ocupamos oportunamente de los procesos de ranurado térmico, concretamente, del ranurado por arco de plasma, de gran utilidad para la reparación de soldaduras ya efectuadas.
Por estar estrechamente relacionadas con la soldadura, desde el momento en que emplean equipos similares consistentes básicamente en una fuente de energía, uno o más cilindros de gas, consumibles y una antorcha con sus cables correspondientes, la AWS denomina las diversas tecnologías de corte y ranurado térmico como procesos afines a la soldadura.
En este artículo, entonces, vamos a presentar todas las técnicas que forman parte de los procesos afines a la soldadura, los cuales, además del corte y ranurado térmico, incluyen un tercer grupo de particular importancia en la industria aeronáutica: el rociado térmico o termorrociado.
Para comenzar, nada mejor que una presentación de estos métodos. Atento a ello, la figura de abajo representa gráficamente todos los procesos afines a la soldadura según la clasificación de la AWS.
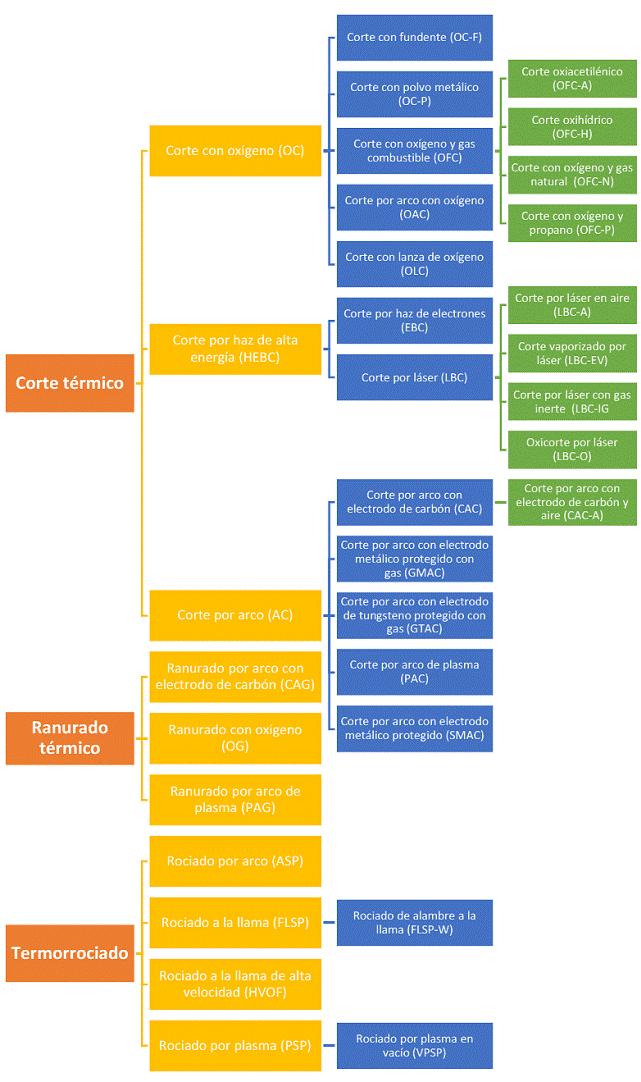
Procesos afines a la Soldadura – Clasificación AWS
Ahora que tenemos un panorama general de estos procesos afines, vamos a revisarlos brevemente, basándonos, nuevamente, en las definiciones que proporciona en cada caso la AWS y manteniendo las siglas originales del inglés con las que se conocen estos procesos en todo el mundo.
Corte térmico (TC)
Cuando hace un tiempo comparamos las diversas tecnologías de corte térmico mecanizado, nos concentramos en las características y prestaciones que brinda cada una (oxicorte, corte láser y corte por plasma) sin detallar qué es el proceso de corte térmico en sí.
Los procesos de corte térmico se aplican en diferentes campos de la ingeniería mecánica, la construcción naval y la tecnología de procesos para la producción de componentes y la preparación de los bordes de soldadura. La norma DIN 2310 clasifica estos procesos de corte térmico según una serie de parámetros que abarcan la física del proceso de corte, el grado de mecanización, el tipo de fuente de energía y la disposición del baño de agua (si corresponde).
Cada uno de estos parámetros conduce a una multiplicidad de subprocesos que sería arduo detallar. Sin embargo, en su definición de corte térmico la AWS tiene en cuenta principalmente la física del proceso cuando hace referencia a “un grupo de procesos de corte que separan o eliminan el metal ya sea por fusión, oxidación (quemado) o vaporización (sublimación) localizada de las piezas”. En cualquier caso, la expansión por un chorro de gas y/o por evaporación es la responsable de la proyección del material fundido y la aparición de productos de reacción en forma de escoria. Los dos procesos de corte térmico más populares son el corte por arco con oxígeno (OAC) y el corte por arco de plasma (PAC), pero veremos que hay muchos más.
De acuerdo con la clasificación anterior, los procesos de corte térmico se dividen en tres subgrupos principales, donde cada uno, a su vez, también presenta diversas categorías.
1) Corte con oxígeno (OC): es un grupo de procesos de corte térmico que corta o elimina el metal por medio de la reacción química entre el oxígeno y el metal base a temperatura elevada, la cual se mantiene mediante el calor de un arco, una llama de oxígeno y gas combustible u otra fuente.
El gráfico siguiente muestra las diferentes opciones del corte con oxígeno según la fuente empleada.

Procesos afines a la soldadura – Corte con Oxigeno
El más usado de este grupo es el corte con oxígeno y gas combustible (OFC), así como sus variantes. El calor de una llama de gas combustible eleva la temperatura del metal hasta su temperatura de autoignición y luego dirige hacia el metal una corriente de oxígeno a alta presión, efectuando el corte (figura de abajo). La temperatura de autoignición de un material es la temperatura a la que puede comenzar la oxidación rápida (combustión) y, por ejemplo, la del acero con oxígeno puro es de 870 °C a 900 °C.
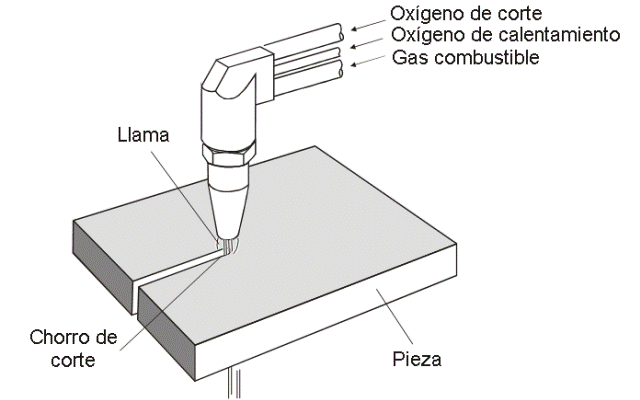
Procesos afines a la soldadura – Corte con oxígeno y gas combustible
Los procesos de OFC se identifican por el tipo de gas combustible usado con el oxígeno para producir la llama de precalentamiento. Comúnmente, el OFC se realiza con el corte oxiacetilénico (OFC-A), es decir, usa acetileno, un gas que tiene la máxima temperatura de llama (aprox. 3000 ºC) aunque también se emplean, en orden decreciente de temperatura de llama, propileno, hidrógeno (OFC-H), gas natural (OFC-N) y propano (OFC-P).
La antorcha de OFC se usa más que cualquier otro proceso de soldadura, abarcando prácticamente todas las áreas, desde manufactura y mantenimiento industrial, hasta aplicaciones en talleres ferroviarios, talleres mecánicos y maquinaria agrícola. No obstante, el OFC es uno de los procesos que más registran aplicaciones erróneas, ya que no se requiere gran pericia para encender la antorcha y efectuar los cortes. Esto no solo puede conducir a cortes de mala calidad, sino que frecuentemente se emplean antorchas poco seguras. Un buen corte por OFC no sólo debe ser recto y cuadrado, sino que prácticamente no debe requerir acabado posterior.
El OFC es el proceso indicado para cortar aleaciones ferrosas. Los aceros con bajo contenido de carbono (hasta 0,3 %) son fáciles de cortar, a diferencia de los aceros de alto níquel, hierro fundido y acero inoxidable, mientras que la mayoría de los metales no ferrosos tales como latón, cobre y aluminio, no pueden cortarse mediante OFC. Tampoco se aconseja usar esta técnica con titanio y magnesio, ya que resulta poco práctica al requerir un complejo acabado posterior.
2) Corte por haz de alta energía (HEBC): es un grupo de procesos de corte térmico que separan o eliminan material por fusión, quemado o vaporización localizados de las piezas mediante un haz con altas densidades de energía. Este haz puede ser de electrones o un rayo láser, y de ahí surgen las dos tecnologías de este proceso, de las cuales el corte por láser (LBC), con sus variantes, es de lejos la más usada.
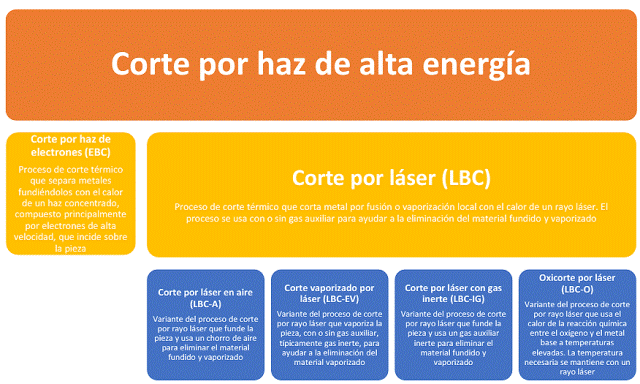
Procesos afines a la soldadura – Corte por Haz de Energía
En el proceso de corte por láser, el material primeramente se funde y luego se dirige un chorro de gas hacia ese material fundido para expulsarlo por la parte inferior del corte. Aunque el láser se usa principalmente para cortar materiales muy delgados, puede emplearse en acero al carbono de hasta 1 pulgada de espesor.
El gas de aporte del LBC puede ser un gas exotérmico o un gas no reactivo y la elección dependerá del material a cortar. Por ejemplo, para aluminio, plástico, madera, materiales compuestos, vidrio y cuarzo se usa aire; para cobre, acero inoxidable y acero al carbono se usa oxígeno; para aleaciones de níquel es común el uso de nitrógeno, y para titanio se usa argón. Los gases no reactivos no añaden calor al proceso de corte; simplemente retiran el material fundido expulsándolo del corte. Los gases exotérmicos reaccionan con el material que cortan, al igual que un soplete de OFC. El calor adicional producido a medida que el gas exotérmico reacciona con el metal ayuda a expulsar el material fundido fuera de la zona del corte.
3) Corte por arco (AC): es un grupo de procesos de corte térmico que corta o elimina el metal por fusión con el calor de un arco entre un electrodo y la pieza.
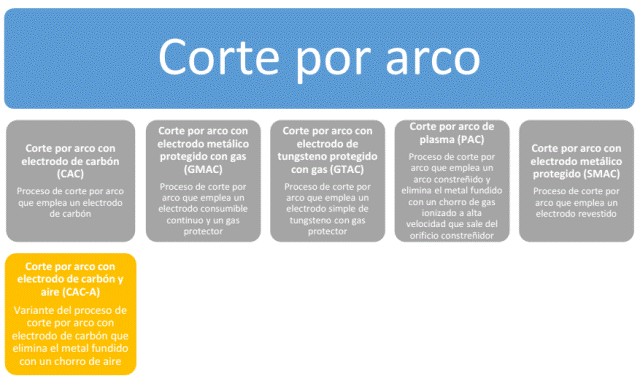
Procesos afines a la soldadura – Corte por Arco
En su oportunidad presentamos varios artículos sobre uno de los procesos más difundidos de este grupo, que es el corte por arco de plasma, explicando el fundamento, presentando los equipos usados en el proceso y destacando la incidencia de esta técnica comparada con otras tecnologías de corte térmico.
Otro proceso muy usado de corte por arco es el que emplea un arco con electrodo de carbón (CAC) y su variante, CAC-A, que usa aire para expulsar el metal fundido del área de corte y, de esa manera, promueve la rapidez, la calidad y la capacidad de control del proceso.
A diferencia del proceso de corte con oxígeno y gas combustible (OFC), que puede aplicarse solamente a metales capaces de ser oxidados rápidamente por la corriente de oxígeno, el corte por arco de carbón y aire (CAC-A) no tiene ese requisito, ya que la corriente de aire sólo expulsa el metal fundido. Esto amplía la variedad de metales que pueden cortarse, que van de aceros al carbono, inoxidables y de baja aleación a aleaciones de cobre, magnesio y níquel, pasando por hierro fundido, aluminio, bronce-aluminio, aluminio-níquel-bronce, y titanio, zirconio, hafnio y sus aleaciones.
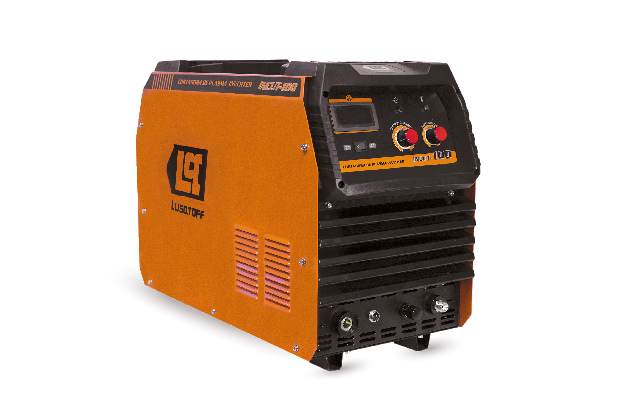
Cortadora de Plasma Inverter
Ranurado térmico (TG)
Esta es una importante variante del proceso de corte térmico que elimina el metal fundiendo o quemando la totalidad de la porción eliminada para formar un bisel o una ranura.
En esta nota brindamos detalles sobre el proceso de ranurado más usado, que es el repelado o ranurado por plasma. Sin embargo, el grupo también abarca otras dos técnicas que comprenden el ranurado por arco con electrodo de carbón y el ranurado con oxígeno.
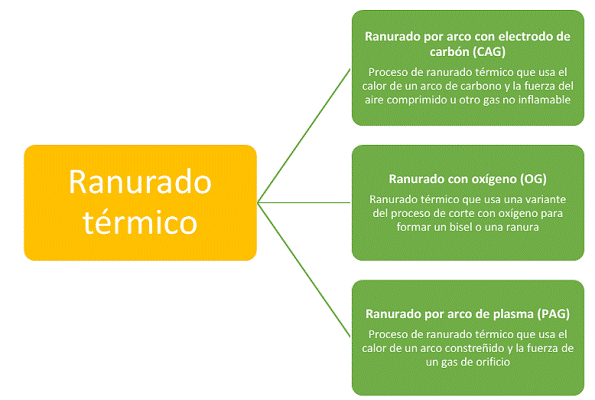
Procesos afines a la soldadura – Ranurado Térmico
En el proceso de ranurado con carbón (CAG) se produce un arco eléctrico entre la punta de un electrodo de carbón y la pieza a ranurar. Se dirige un chorro de aire paralelo al electrodo para expulsar el metal fundido del área del arco, formándose así una ranura. Este proceso se usa con aceros al carbono, aceros inoxidables, aluminio, aleaciones de níquel y fundición de hierro y de cobre. Es un proceso de fácil aprendizaje y ofrece altas tasas de remoción. También es un proceso altamente ruidoso y produce grandes cantidades de humo. La calidad de la ranura es de difícil control y pueden producirse depósitos e inclusiones de carbón en el metal base.
El ranurado con oxígeno (OG) emplea gas combustible en un proceso térmico-químico. El acero se calienta a su temperatura de ignición con un soplete de corte con oxígeno y gas combustible, y luego se oxida rápidamente y se expulsa de la superficie por medio de un chorro de oxígeno. Este proceso ofrece bajo nivel de ruido, mejor portabilidad y mayores velocidades que los procesos de corte mecánicos. Sin embargo, no sólo disminuye el control preciso sobre la ranura y presenta menor velocidad que el ranurado con carbón, sino que al basarse en la combustión, su uso se limita a los aceros al carbono.
Termorrociado (THSP)
Este es un grupo de procesos en los que diversos materiales de recubrimiento, tanto metálicos como no metálicos y finamente divididos, se depositan en estado fundido o semifundido sobre un sustrato para formar un depósito de termorrociado. El material de recubrimiento puede estar en forma de polvo, varilla, cable o alambre. Puesto que el metal fundido se acompaña con una corriente de aire, la pieza a rociar no se calienta apreciablemente, por lo que el termorrociado se conoce como un método «frío» de deposición metálica.
La fuente de calor para fundir el material puede ser una llama de oxígeno y gas combustible, un arco eléctrico o una llama de plasma, y en base a ello se presentan las distintas variantes del proceso que vemos en el siguiente cuadro.
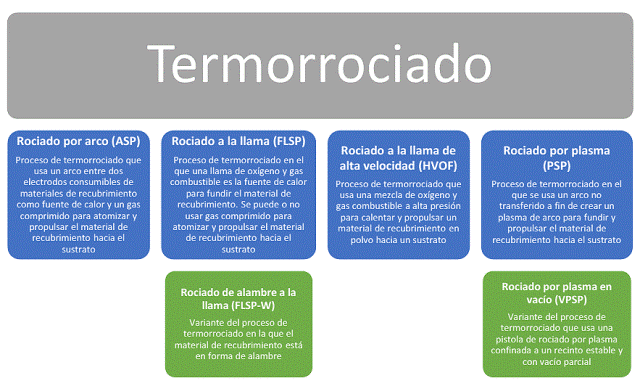
Procesos afines a la soldadura – Termorrociado
El rociado por arco (ASP) usa los mismos principios empleados en los sistemas de soldadura por arco con electrodo consumible. El material de recubrimiento, en forma de alambre, se carga eléctricamente y luego establece contacto para crear un arco. Las gotas fundidas del alambre se rocían sobre el sustrato con una corriente de aire a alta velocidad para atomizar y propulsar el material (ver figura de abajo). Los recubrimientos por ASP son muy rentables y se usan normalmente para aplicar metales como aluminio puro, zinc, cobre, y aleaciones como acero inoxidable. También permite efectuar ajustes para lograr una variedad de texturas de recubrimiento (200-800 micropulgadas).
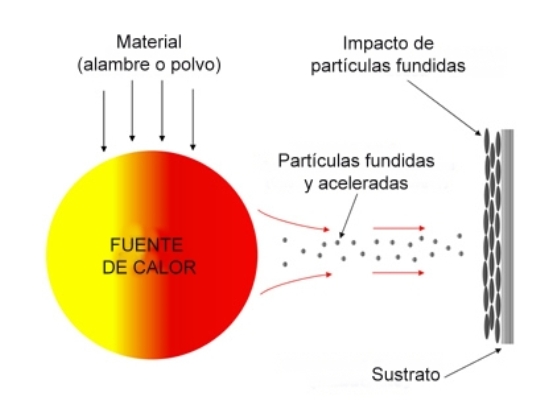
Procesos afines a la soldadura – Rociado por Arco
El rociado a la llama es la técnica original de termorrociado desarrollada hace unos 100 años. Usa los principios básicos de un soplete de soldadura con la adición de una corriente de aire a alta velocidad para propulsar las partículas fundidas sobre el sustrato. El material de recubrimiento puede estar en forma de polvo (técnica FLSP) o alambre (técnica FLSP-W).
El rociado a la llama de alta velocidad (HVOF) quema oxígeno y un gas inflamable tal como propano, propileno o hidrógeno. Aunque el sistema HVOF usa el principio básico de la combustión, la pistola de rociado está diseñada de manera diferente a la de la pistola de rociado FSLP, a fin de producir altas temperaturas de llama y mayores velocidades. Esto posibilita una fusión más completa del polvo y más energía cinética disponible para «aplanar» las partículas fundidas del material de recubrimiento. El proceso HVOF es el más usado para aplicar metales de alta temperatura de fusión y aleaciones metálicas, tales como carburo de tungsteno, Inconle®, carburo de cromo, Stellite® y Tribaloy®.
El rociado por plasma (arco no transferido) usa gases inertes alimentados a través de un electrodo para inducir gases plasmanógenos. Cuando estos emergen de la boquilla de la pistola y vuelven a su estado normal, se libera una gran cantidad de calor. A su vez, un material de recubrimiento en polvo se inyecta en la llama plasmanógena y es propulsado sobre el sustrato.
Los recubrimientos cerámicos de diversos tipos son los que aplican con mayor frecuencia mediante rociado PSP debido a sus altas temperaturas de fusión, que superan los 2000 ºC.
Los recubrimientos aplicados mediante las diversas técnicas de termorrociado ofrecen más versatilidad, ya que puede usarse una gran variedad de materiales de recubrimiento (carburos de tungsteno, acero inoxidable, cerámicas (óxido de cromo, óxido de aluminio, zirconio y titanio), carburos de níquel-cromo y metales puros (aluminio, zinc, cobre) en una multiplicidad de sustratos, tales como aluminio, acero, acero inoxidable, cobre, bronce y algunos plásticos.
En futuros artículos vamos a expandir algunos de estos procesos afines a la soldadura mencionados en esta nota, a fin de conocer más detalles sobre su modo de uso y sus aplicaciones en diversos campos.
6 Comentarios
Rene Padron
Este es el trabajo de mi vida lo que me gusta hacer estoy en Venezuela Maturin EDO Monagas con el cargo de Fabricador y le he hecho trabajado a muchas Empresas y a PDVSA He visto su modo de trabajo la esperiencia y la verdad que me llama la atencion.El lugar donde estan fabricando los tanques,si me dieran la oportunidad de trabajarle a su Empresa no se arrepentirian, por que me encanta el trabajo y la verdad quisiera trabajar en otro Pais que valoren mi trabajo me gusta escuchar a los demas y que me escuchen para asi expresar mis ideas y asi desenvolverlas ,he fabricado tanques,fractan ,estructuras,quemadores si se comunicaran conmigo les mandaria algunas de las fotos que he fabricado gracias les agradezco su mas sinceras atencion .TELF:02916432265 /04128582571
MarcoAntonio
Que buen articulo, muy muy prolijo. Felicitaciones y gracias por compartir conocimiento.
Saludos!
Osvaldo
Insto a que sigan compartiendo este tipo de artículos los Felicito y muchas gracias
demaquinasyherramientas
Un gusto Osvaldo, gracias por lo saludos!
Pingback: Soldadura Inverter | De Máquinas y Herramientas
Pingback: Soldadoras TIG AC/DC vs DC Cuál comprar | De Máquinas y Herramientas
Susana Maltese
Me encantó el artículo…Felicitaciones!!!
demaquinasyherramientas6
A vos Susana! Gracias por participar, y por leernos!