La elección del alambre para soldadura es un factor importante para el éxito al soldar distintas piezas entre sí, pero todavía falta conocer cuál es la relación entre el parámetro feed y el rendimiento.
Cuando la velocidad del alambre (parámetro feed) está incorrectamente establecida, podemos tener una soldadura cuyo aspecto es bueno pero que en realidad ha penetrado poco o demasiado, lo cual es un problema. Por el contrario, cuando la velocidad (y por lo tanto la corriente eléctrica) es la adecuada, la soldadura se verá bien y será buena mecánicamente hablando.
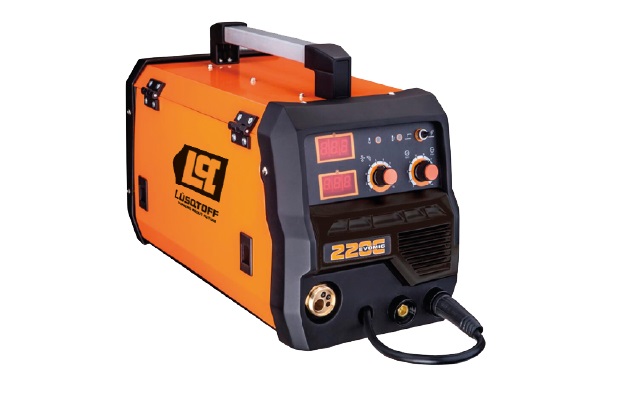
Soldadora Inverter EVO MIG-220
En este artículo asumimos que el lector conoce de antemano la técnica de soldadura MIG, que las piezas a soldar están correctamente preparadas y limpias, que el equipo es el apropiado para la soldadura que se intentará realizar y que se ha escogido el electrodo y el gas adecuado (si corresponde).
Elección de la correcta velocidad de feed del alambre para soldadura
Sabemos que la gran mayoría de las máquinas MIG son de voltaje constante (CV), por lo que este no es un parámetro a tener en cuenta. Sabemos también que la correcta elección del diámetro y material del electrodo se puede establecer de acuerdo al material por medio de tablas prediseñadas. Por último, sabemos que lo ideal es llevar la velocidad a su mínima expresión posible sin afectar la soldadura.
Cada equipo de soldadura tendrá sus propios parámetros ya que no existen dos soldadoras que otorguen la misma potencia exacta de salida; aún así es posible obtener valores lo suficientemente aproximados como para lograr buenos resultados la primera vez, y un buen rendimiento. A partir de allí será cuestión de experimentar con cada combinación de material y alambre para soldadura.
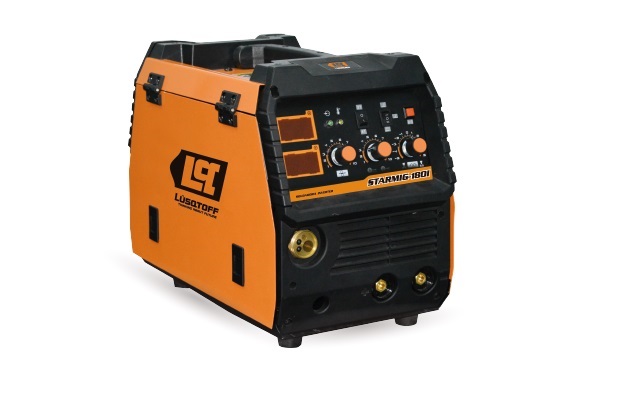
Soldadora STARMIG 180I
Cálculo del feed
Primero es necesario medir el espesor de las piezas a unir. Como regla general, por cada 25 centésimas de milímetro (0,25 mm) es necesario incrementar en 10 amperes la corriente. Tenga en cuenta que el espesor está calculado para piezas sin chaflanes o biseles. Si las piezas han sido preparadas con biseles (cortes en V), divida por dos el espesor de la pieza.
Luego se determina el coeficiente A de acuerdo al diámetro del alambre para soldadura; este coeficiente A se multiplicará por el amperaje, y el resultado nos dará la velocidad necesaria del alambre, en milímetros por minuto. En la siguiente tabla se ofrecen algunos ejemplos.
Diámetro del alambre en mm | Coeficiente A | Velocidad, en cm/min, para planchuelas de 3,175 mm | Velocidad, en cm/min, para planchuelas de 10 mm |
0,584 | 350 | 1111,25 | 3500 |
0,762 | 200 | 635 | 2000 |
0,889 | 160 | 508 | 1600 |
1,143 | 100 | 317,5 | 1000 |
Problemas derivados de la elección incorrecta del feed del alambre para soldadura
Una buena soldadura se destaca por su aspecto y por la penetración en el material, apreciable al realizar un corte en sección. Las defectuosas, por otro lado, se verán demasiado anchas (si la velocidad del feed es excesiva) o muy angostas (si la velocidad del feed es insuficiente).
Al aplicar poco voltaje no logramos una buena temperatura de trabajo, por lo que la soldadura será fría, y no alcanzará a penetrar correctamente. Por el contrario, una tensión excesiva causará también un exceso de temperatura, y la soldadura aparecerá salpicada y esparcida. En ambos casos no habrá una penetración coherente a lo largo del metal.
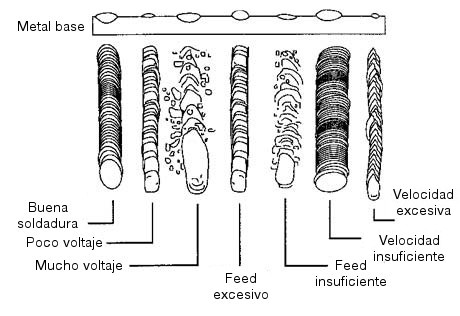
Diferencias entre una buena soldadura y una mala.
Pasemos a ver los problemas derivados de las dos velocidades que manejamos al soldar: el feed del alambre para soldadura, y el avance de la antorcha sobre la costura.
Si aplicamos demasiada velocidad al feed de alambre, además de desperdiciarlo y ocasionar frecuentes atascos en la boca de la antorcha, tendremos una soldadura acordonada, demasiado cilíndrica; esto provoca que haya material de aporte sobrante, que luego deberá descartarse, con lo que se desperdiciará alambre para soldadura.
Si aplicamos poca velocidad podemos tener problemas de fusión del alambre en la boca de la antorcha; pero si esto no alcanza a suceder, la costura será pobre, demasiado plana y sin penetración, con salpicaduras laterales.
Finalmente, una velocidad de avance insuficiente dará lugar a una soldadura apretada, ancha y con exceso de material en la parte superior. Una velocidad de avance excesiva producirá una soldadura angosta, demasiado pequeña y no dará oportunidad a que el material de aporte funda y penetre adecuadamente.
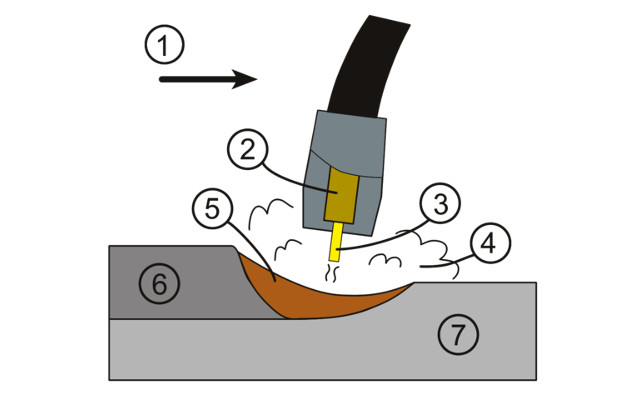
Diagrama MIG
Buenas prácticas a la hora de soldar
La tabla que vimos anteriormente debe tomarse como una guía general. Los valores, por supuesto, variarán de acuerdo al material de las piezas a soldar, al material del alambre, a la velocidad de avance de la antorcha e incluso variarán de acuerdo al voltaje y hasta del gas inerte que utilicemos.
Lograr el máximo rendimiento del alambre para soldadura es más bien un arte antes que una técnica que pueda replicarse en cualquier taller o fábrica. Cada operario sabrá encontrar los parámetros ideales de soldadura con la práctica, por lo que se recomienda siempre llevar un cuaderno en donde se anoten los parámetros junto a los resultados obtenidos.
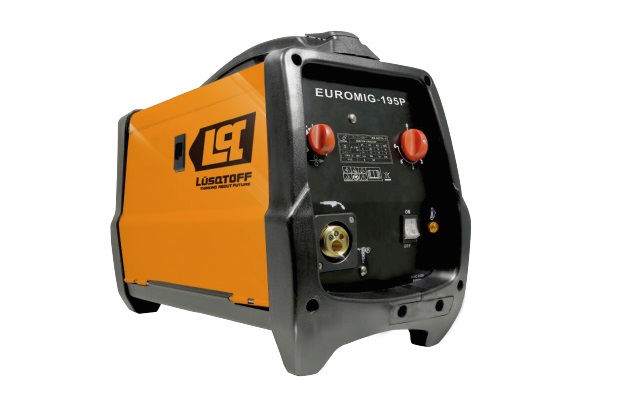
Soldadora MIG/MAG EUROMIG 195P
Al hacer uso de la tabla provista en este artículo el operador podrá obtener los parámetros de velocidad y amperaje aproximados; a partir de allí, y dependiendo de la máquina utilizada —algunas administran automáticamente el voltaje de trabajo, mientras otras permiten ajustarlo manualmente— se podrá afinar la velocidad del feed hasta llevarla al mejor valor posible.
Aunque parezca increíble, es importante también tener en cuenta la dirección en la que se realizará la soldadura; no es lo mismo soldar de derecha a izquierda que de izquierda a derecha. Un soldador experimentado procurará siempre —si es diestro— hacerlo de derecha a izquierda, ya que se logra así un cordón más prolijo y una mayor penetración del material de aporte.
Un Comentario
Pingback: Soldadura SMAW (qué es y procedimiento) | De Máquinas y Herramientas
Pingback: Procesos de Soldadura | De Máquinas y Herramientas
CLAUDIO
me interesaría saber como calcular el coeficiente A