Durante estos últimos 15 años, los discos flap han sido la categoría de abrasivos de mayor crecimiento en la industria metalmecánica y otras. Las razones de su vertiginoso avance son varias.
Desde el punto de vista del desempeño del producto, ofrecen un rápido arranque de viruta y proporcionan operaciones de amolado, desbarbado y acabado con un solo producto y a un menor costo total. También son capaces de efectuar un corte limpio con menos recalentamiento, agrietamiento y quemado que los discos abrasivos comunes.
Desde el punto de vista del usuario, gozan de amplia preferencia por ser más livianos, más fáciles de controlar y requieren menos tiempo de inactividad entre un cambio y otro. No menos destacable es la reducción de la vibración y la consiguiente fatiga, así como la reducción del ruido.
Con todos estos beneficios que hoy en día ofrecen los discos flap, es importante conocerlos con mayor profundidad para luego saber elegirlos adecuadamente para nuestros proyectos. Por lo tanto, en este artículo vamos a comenzar por la primera parte para enterarnos de la información básica que caracteriza a un disco flap.
¿Cómo está compuesto un disco flap?
Precisamente la denominación de esta herramienta de corte responde a su propia estructura. Los discos flap presentan un recubrimiento de material abrasivo que adhiere los granos -los mismos tipos de grano que se encuentran en los abrasivos aglutinados- a una placa de soporte, que como veremos más adelante puede ser de diversos materiales. Después, esta placa de soporte se corta en láminas más pequeñas y se apila radialmente en múltiples capas para formar un disco de láminas, solapas o aletas (del inglés «flap») que de esta manera quedan unidas a un núcleo central.
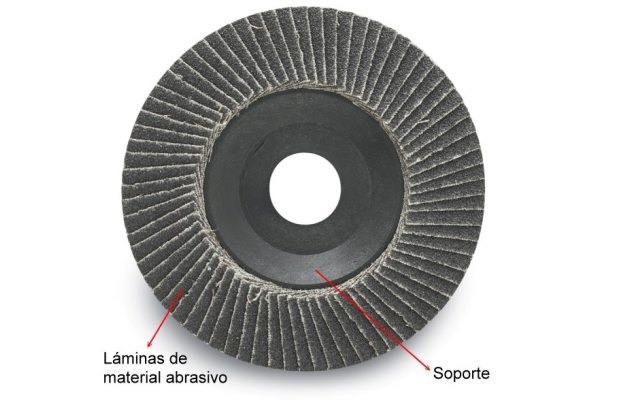
Disco Flap
Si bien los primeros discos flap para amoladoras angulares de alta velocidad se desarrollaron hace unos 40 años y eran más bien básicos, las versiones actuales ofrecen una gran diversidad. Para muchos entendidos, si lo que buscamos es un acabado superior y una mayor facilidad de uso durante la operación, el disco flap supera ampliamente a la muela abrasiva común.
Esta afirmación responde a la serie de ventajas que incorporan los discos flap, los cuales si bien son más costosos que una muela abrasiva, a la larga la mayor inversión se traduce en un mejor rendimiento. Examinemos algunas de las ventajas de los discos flap.
- Diseño ligero que reduce la fatiga del usuario.
- Fáciles de usar porque requieren muy poca presión superficial.
- El corte en frío permite un contorneado ligero y evita que el disco se queme.
- Mayor vida útil, ya que resisten el desgaste hasta 10-15 veces más que los discos convencionales gracias al diseño de solapas superpuestas.
- Eliminación agresiva del material, igualando la performance de las muelas abrasivas de centro deprimido, pero ofreciendo mayor seguridad, ya que no requiere usar la guarda protectora de las amoladoras.
- Rendimiento consistente, ya que continuamente se exponen granos nuevos durante la vida útil del disco.
- El esmerilado y acabado en un solo paso reduce costos y tiempo de inactividad.
- El ángulo de rectificado de forma cónica proporciona un contacto óptimo entre la pieza de trabajo y la superficie del disco.
- La construcción robusta permite un amolado agresivo de los bordes, sin agrietamiento ni rotura del disco.
Como expresamos más arriba, los discos flap consisten básicamente en un soporte y una serie de láminas de material abrasivo dispuestas radialmente. Tanto el soporte como el material abrasivo pueden ser de diversos materiales y características, posibilitando una amplia variedad de discos flap indicados para cada uso. Veamos entonces cuáles son esas variedades.
Tipo de soporte
El material de la placa de soporte para un disco flap es una variable importante que determina su aplicación. Los materiales más comunes son los siguientes:
Fibra de vidrio: más resistente, duradera, liviana y segura, la fibra de vidrio es actualmente el más popular de los soportes, ya que crea una unión fuerte con los adhesivos y no contamina la superficie de trabajo. Este tipo de placa se consume durante el uso y absorbe muy bien la vibración. El soporte de fibra de vidrio está constituido por capas de fibra de vidrio unidas en un entramado y presionadas entre sí. Cuantas más capas haya y mayor sea la densidad de la malla, el soporte será más fuerte y duradero, por lo que esta es una consideración a tener en cuenta cuando se examinan las especificaciones detalladas de un disco flap.
Plástico: casi tan popular como el anterior, el soporte de material plástico, y particularmente nylon, tiene muchos adeptos. Los soportes de plástico tienen la ventaja de poder recortarse, lo que permite un uso más prolongado de las láminas, especialmente durante el desbarbado y acabado. En la actualidad, el plástico se está convirtiendo en una opción cada vez más atractiva debido a su conformabilidad y bajo costo.
Metal: las placas de soporte metálico, comúnmente de aluminio, son la opción más segura y presentan propiedades excelentes cuando se necesita firmeza y fuerza adicional. Dado que las placas de metal son costosas, deben usarse cuando el gasto lo justifique, por ejemplo, cuando trabajamos en aplicaciones en hormigón o piedra. El soporte metálico no se consume durante el uso, pero las placas se pueden reciclar fácilmente cuando el disco termine su vida útil.
Tipo de abrasivo
Aunque los discos flap conocieron su auge gracias a la industria del metal, se pueden usar para una gran variedad de aplicaciones, ya sea en metal o madera, rectificado o acabado de hormigón, alisado o acabado de piedra, remoción de pintura u óxido, y muchas más. El material que compone el grano abrasivo de un disco flap es fundamental para nuestras necesidades específicas de trabajo y puede ser de varios tipos. Seguidamente presentamos los más comunes, aunque hay más.
Óxido de aluminio: este es el material original que se usaba para el amolado de metales en los años ’70, cuando se introdujeron por primera vez los discos flap. También es la opción de menor costo. Hoy en día el abrasivo de óxido de aluminio se recomienda para trabajos pequeños donde la exigencia de calidad es de baja a intermedia.
Zirconio: caracterizado por sus buenas propiedades térmicas, dureza y alta resistencia al desgaste, su mayor costo garantiza un uso prolongado y un menor tiempo de inactividad, por lo que supera en prestaciones al óxido de aluminio y es actualmente el material más usado para el mecanizado de metales. Normalmente se emplea para trabajos de amolado y acabado de acero en general, que también incluye aplicaciones en acero inoxidable.
Carburo de silicio: la forma mineral natural del carburo de silicio es alargada, delgada y filosa, así que podemos imaginar un disco flap de carburo de silicio como recubierto por miles de cuchillas diminutas, pero muy afiladas. Generalmente, los abrasivos de carburo de silicio son ideales cuando se necesita un corte limpio en metales no ferrosos como latón, aluminio o titanio, así como en otros materiales como piedra natural, ladrillo, baldosas, madera, cuero y vidrio, aunque no son muy efectivos en aplicaciones que exigen una alta presión sobre el disco.
Óxido cerámico: tiene una estructura microcristalina y más uniforme que la de los abrasivos de óxido de aluminio o zirconio, lo que le permite romperse de manera controlada ampliando la gama de aplicaciones disponibles. Sin embargo, es importante tener en cuenta que los abrasivos cerámicos son particularmente sensibles al calor y a la presión, lo que significa que es esencial un proceso correctamente diseñado para su uso exitoso. Al mismo tiempo, los óxidos cerámicos están demostrando una excelente performance en piezas fundidas de aluminio, acero dulce, en el acabado del acero inoxidable y en muchas de las aleaciones de titanio comúnmente usadas en aplicaciones aeroespaciales.
Características del material abrasivo
a) Densidad
Cuando hablamos de densidad del abrasivo debemos pensar en el área abrasiva total proporcionada por las láminas de un disco flap. Esta área depende de la cantidad de láminas presentes en un disco, su ángulo con respecto al centro del disco y la distancia a la que están espaciadas. Cada una de estas variables puede afectar el área total del disco que estará en contacto con la pieza de trabajo. A tal efecto, podemos distinguir dos tipos de densidades:
Densidad estándar: las láminas de densidad estándar son óptimas para una rápida remoción de material y aplicaciones de trabajo pesado.
Alta densidad: las láminas de alta densidad son las más adecuadas cuando se trabaja en piezas curvas o irregulares, así como durante el acabado.
Sin embargo, como planteamos más arriba, para diferenciar correctamente entre dos discos que pueden llevar la especificación «láminas de densidad estándar» o «láminas de alta densidad», en lugar de fijarnos meramente en su calificación de densidad debemos considerar siempre el número, el ángulo y el espaciado de las láminas en su conjunto.
b) Grano
Todos aquellos que trabajan con muelas abrasivas están familiarizados con el tamaño de grano. Los discos flap no son la excepción. Los tamaños de grano van de grano grueso (número bajo) para desbaste, hasta grano fino (número alto) para acabado, pasando por un valor intermedio para el lijado convencional.
El siguiente gráfico muestra los usos recomendados para cada tamaño de grano y de densidad del abrasivo.
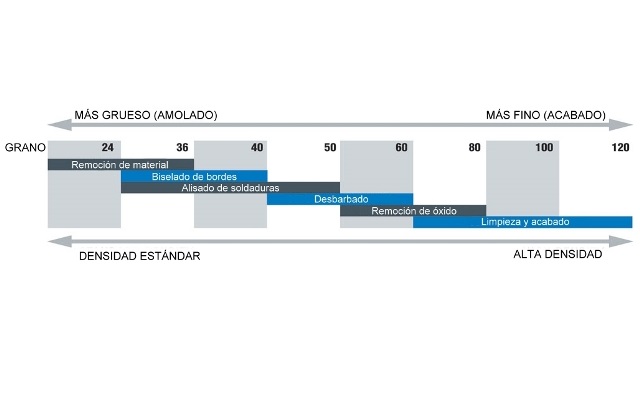
Discos Flap – Usos recomendados
Formas de los discos flap
Los discos flap están diseñados para usarse en amoladoras angulares, lo que les permite trabajar en un ángulo poco profundo o incluso plano con respecto a la superficie de la pieza de trabajo. El ángulo que forman las láminas del disco con la pieza incidirá directamente en la agresividad del corte.
A tal efecto, hay dos diseños básicos que debemos conocer y que presenta la figura de abajo:
- Discos planos (conocidos como Tipo 27)
- Discos cónicos (conocidos como Tipo 29)
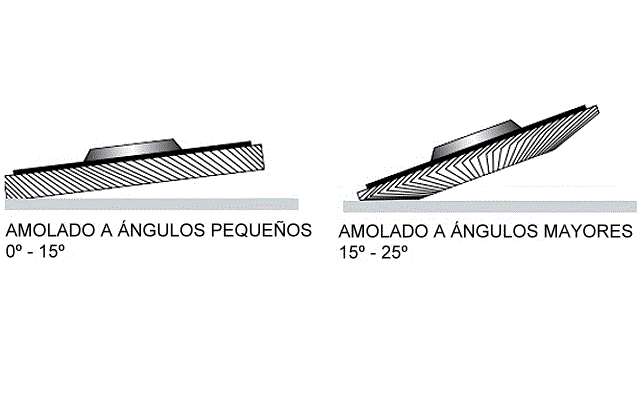
Discos Flap – Diseños básicos
Discos planos: son generalmente preferidos para aplicaciones de acabado o amolado más controlado en las que se aplica una menor presión al disco. Tienen una superficie de amolado lisa y se usan principalmente para trabajar en superficies planas y esquinas exteriores. El ángulo entre el disco y la pieza de trabajo varía entre 0 y 15º, pudiéndose amolar y pulir al mismo tiempo, lo cual reduce la carga de trabajo. Los discos de tipo 27 también pueden ser de forma convexa o de centro deprimido, permitiendo una mayor superficie de contacto entre el disco y la pieza de trabajo.
Discos cónicos: en este caso las láminas están dispuestas en ángulo, por lo que los discos ofrecen una mayor área de superficie para la extracción de material en superficies horizontales, ya que durante el funcionamiento el disco forma un ángulo de 15° a 25° con la pieza de trabajo. Esto los hace ideales cuando se requiere la remoción de gran cantidad de viruta en poco tiempo. También se pueden usar para trabajos de contornos y bordes o cantos.
Una vez que adquirimos y comprendemos estos conocimientos, estaremos en condiciones de decidir cuál es el disco flap adecuado para nuestro propósito. En un próximo artículo puntualizaremos los detalles a tener en cuenta para ayudarnos a una elección exitosa.
2 Comentarios
IRIS
SOLICITAMOS SU COTIZACION POR DISCOS FLAP 4-1/2 115MM PRECIO POR MAYOR
modales
hola, buen día, cómo está?… un poco de modales no viene mal, jajaja