La tecnología Direct Torque Control (también llamada control de par directo o control directo de torque) se encuentra cada vez en más máquinas herramienta eléctricas que hacen uso de un motor trifásico. Es un sistema que permite variar arbitrariamente tanto la velocidad como el torque del motor por medio de un microprocesador que determina el par motor (M) y el flujo (Ψ).
En este artículo veremos en detalle qué es esta tecnología, qué usos tiene y qué provecho se le puede sacar en el taller o fábrica.
Direct Torque Control: ¿qué es?
Se trata de un sistema que permite variar el torque o la velocidad de un motor trifásico de inducción, a través de un microcontrolador que mide constantemente dos parámetros (motor y flujo), ajustándolos de acuerdo a las mediciones y sin necesidad de instalar un tacómetro o encoder.
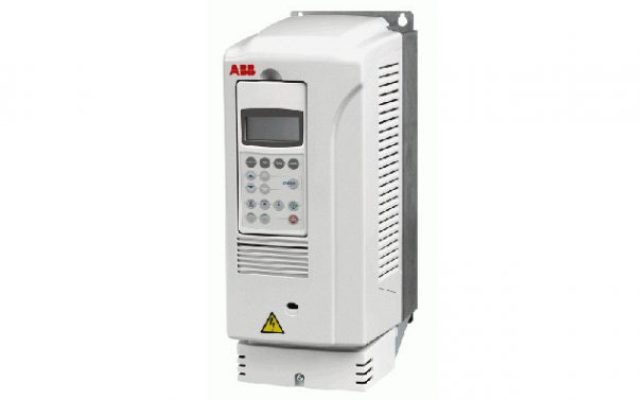
DTC – Unidad
Esta tecnología apareció en Estados Unidos y Alemania a mediados de la década del 80, bajo el nombre Direct Self-Control (DSC), y una de sus primeras implementaciones masivas se dio en las locomotoras Diesel-eléctricas MaK-ABB DE502 alemanas. Inmediatamente después se comenzó a implementar en la industria modificando los variadores de velocidad.
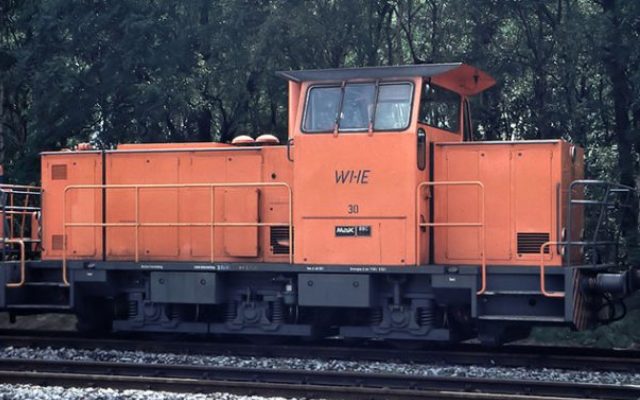
MAK-DE-502
Para entender la mecánica detrás de este proceso, necesitamos saber que un motor eléctrico, dada una velocidad, si se mantiene esta fija, variará el torque en el eje de acuerdo a la carga; y, si el torque se mantiene constante, variará la velocidad. Esta energía está en relación directa a la tensión y el voltaje entregados al motor y, por supuesto, al factor de potencia.
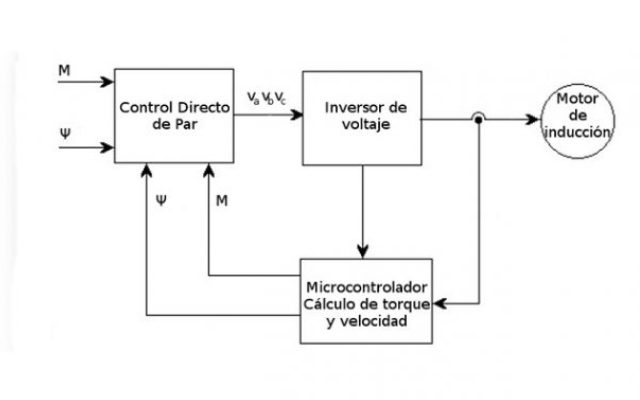
DTC – Esquema
Existe una tecnología anterior a ésta: PWM (por Pulse-Width Modulation, o modulación del ancho de pulso), cuya principal desventaja es la falta total del control sobre el torque, ya que el sistema utiliza como factores de modulación la tensión y la frecuencia, y además requiere la instalación de un encoder o tacómetro para conocer la posición del rotor.
En definitiva: esta tecnología es superior a su predecesor, el variador por tensión y frecuencia, y más económico, ya que no requiere la instalación de encoders (lo que obligaría además a modificar el eje para poder albergarlo).
Ventajas
- Permite un control muy preciso sobre la velocidad o el torque en motores de inducción de corriente alterna trifásica.
- La relación corriente eléctrica/par motor es lineal con DTC: si se incrementa la corriente en un 200%, el par se incrementará en igual proporción; en motores sin DTC la relación no es lineal, y se alcanza un 150% de par como máximo.
- Se obtienen velocidades de frenado mayores, sin necesidad de frenos mecánicos.
- No se producen detenciones por sobrecargas falsas.
- La respuesta de par puede llegar a ser inferior a 1 ms.
- La precisión en la velocidad puede llegar a ±0,1%.
Desventajas
- A bajas RPM el sistema tiende a hacer vibrar el motor.
- Es efectivo con motores de hasta 15 kW; en motores más grandes aparecen algunos problemas como la distorsión de la trayectoria del flujo.
- No es sencillo conectar varios motores en paralelo.
¿Para qué sirve?
En la industria es muy importante contar con un sistema de control de velocidad o de torque; por ejemplo, para la fabricación de papel, es necesario controlar el torque ejercido por el tambor, para lograr la mayor homogeneidad posible en el espesor. En otras aplicaciones, como el mecanizado, también es importante mantener constante la velocidad de giro, para lograr buenos resultados en los procesos de arranque de viruta.
Los mejores resultados se ven en aplicaciones en donde los motores de inducción de hasta 15 kW trabajan en un régimen de velocidades medias o altas; en velocidades bajas el sistema no es tan eficiente, ya que se producen vibraciones indeseadas en el motor.
En definitiva, para los usos industriales convencionales, la tecnología Direct Torque Control permite incrementar al máximo la potencia reduciendo al mínimo las perturbaciones provocadas por las fluctuaciones en la tensión, la corriente y la frecuencia.
Permite el control directo del torque, logrando, independientemente de la velocidad, el par motor máximo, incluso en regímenes de velocidad inferiores a las 100 RPM. Para ello sólo es necesario instalar el variador y reemplazar los contactos por otros capaces de soportar las elevadas corrientes que se generan al arranque.
Algunos usos prácticos
Las máquinas herramienta de taller, tales como tornos, fresadoras, mortajadoras, tupíes, balancines y otros pueden aprovechar esta tecnología para mejorar el control de la velocidad o del torque, con el fin de que los procesos presenten resultados coherentes a lo largo de toda la cadena de producción, y sean fácilmente repetibles en un taller u otro (algo crítico cuando se trata de terminación de superficies, por ejemplo).
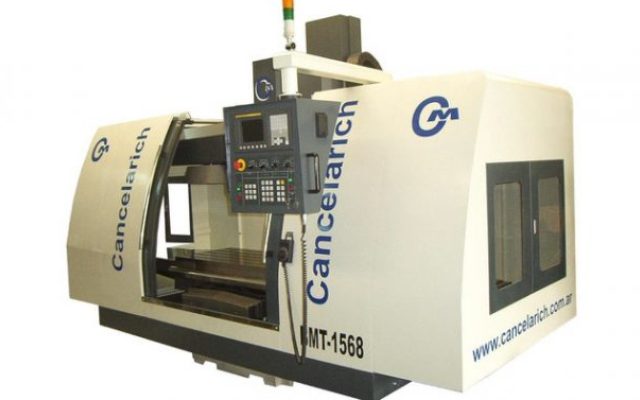
DTC – Centro de mecanizado
Además de estas máquinas, este dispositivo encuentra un uso intensivo en el transporte ferroviario (locomotoras, coches motor, trenes eléctricos), en ascensores, grúas, trituradoras de piedra y otros áridos, extrusoras y un sinfín de otras herramientas o utilitarios.